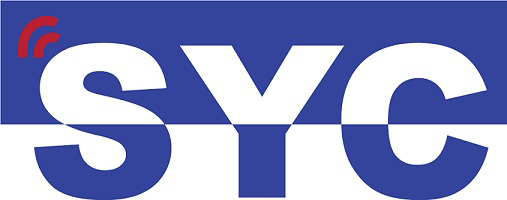
In today's context of rapidly rising labor costs and an emphasis on product quality and safety, automation has become one of the key priorities for planning across various industries.
Unlike the automatic spot welding equipment on the market that simultaneously dispenses solder and drops the iron head.
With a heating rate of 100°C per second and a consistently stable heat source, it is the fastest in spot welding. It performs exceptionally well for products with rapid heat dissipation or challenging soldering requirements (e.g., heat sinks, magnet wires).
This feature ensures that, under automated concepts, each welding position (heating location) remains consistent. With normal cleaning and maintenance, it can be used for over a year, not only saving on consumables but also significantly reducing the production line time needed for recalibrating equipment whenever the welding head is replaced.
By using a covered approach to heat the cut solder wire, the likelihood of solder ball ejection is significantly reduced, and the flux is effectively controlled and directed to the solder joint.
Analyze the required amount of solder for each solder joint based on product solder point experiments. After cutting the solder, proceed with welding to ensure uniform solder quantities at each point, preventing issues of excess or insufficient solder that can lead to quality inconsistencies.
By analyzing the heating time differences required for solder wires from various brands through experiments, and utilizing the equipment's air flow, the flux is efficiently directed to the solder joint holes and the back pad, ensuring complete cleaning of solder joint oxides and achieving 100% hole filling.
Each solder joint has different copper foil contact sizes when viewed microscopically, resulting in varying thermal energy requirements. By controlling 16 parameters for each solder joint, the quality is maintained, reducing the need for subsequent manual rework.